Ultrasonic Impact Treatment(UIT) were invented in Russia in 1972. It has been the subject of considerable research to substantiate the beneficial effects with respect to fatigue performance. Institutions in PRC including Tianjin Univesity(Peiyang Univesity)and in the USA including Lehigh University and the Laboratory of Steel Structures and have conducted research aimed at improving the fatigue performance of highway structures such as steel bridges, traffic signals and light poles. Such work has demonstrated that the fatigue performance of as-welded structures can be improved through the use of UIT.
UIT equipment consists of a power control and a ultrasonic impact gun as is shown below. UIT works by converting harmonic resonations of an acoustically tuned body energized by an ultrasonic transducer into mechanical impulses imparted into the surface of the material being treated. In the conversion process the energizing ultrasonic transducer has a frequency of 20 kHz
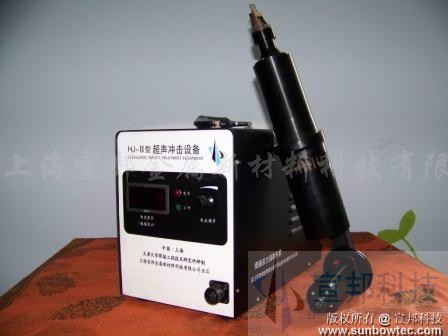
Fig.1 Power control& ultrasonic impact gun
Ultrasonic impact treatment is a mechanical method that can be applied to a weld to reduce tensile residual stresses and locally modify the weld geometry to improve fatigue performance and prolong fatigue life. Furthermore, it can even reshape the appearance of welding toe and intensify the strength by surface engineering as is shown below.
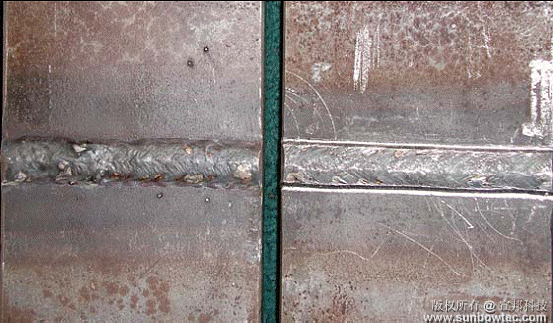
Fig.2 Comparison of welding toe before and after UIT
UIT is carried out on the toes of welds where it modifies the toe shape, reducing the acuity of the mechanical notch. The UIT tool creates a zone of residual compressive stress at the weld toe where stress concentration is greatest for residual and applied tensile loads. 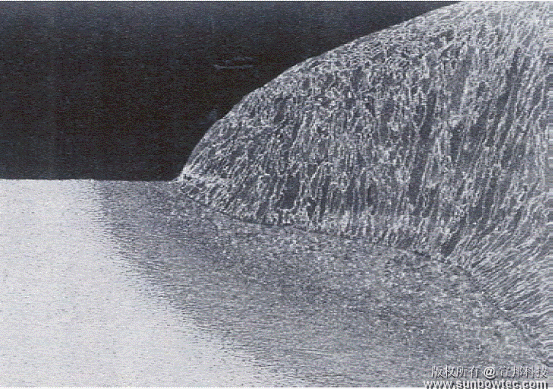 
Fig.3 Comparison of micro appearance of welding toe area before and after UIT
The following list describes the beneficial effects that can result due to treatment. The controlled action of the application allows one to define the exact combination of effects listed below by altering the configuration of the control and treatment parameters. Thus, the user only gets those effects that are desired.
|1| Formation of a white layer up to 10 microns in depth with exceptional corrosion resistance, abrasion resistance, and lubricity.
|2| Plastic deformation of the surface.
|3| Elimination of tensile stress and the introduction of favorable compression stress up to 12 millimeters in depth.
|4| Altering the surface finish resulting in a smoother surface and eliminating defects.
|5| Improvement in endurance and corrosion resistance. Up to 250% and 400% respectively.
These changes in material characteristics provide substantial improvements in both the utilization and manufacturing of metal structures. These include:
|1| Increased operational life in applications subject to dynamic loads or aggressive environments.
|2| Reduced maintenance cost of metal structures subject to corrosion-fatigue destruction.
|3| Decreased cost of manufacturing and operation through the use of less material.
|4| Increased use of high strength steel alloys previously limited by weld properties.
|5| Increased structural stability during manufacturing and operation.
|6| Operational and maintenance cost reduction.
|