一、前言 近几年来随着铝行业的发展,新建的氧化铝厂越来越多,旧厂改造扩建的也不少,可是氧化铝厂的蒸发设备发生应力腐蚀的现象一直没有得到解决。 山西铝厂大蒸发器投产36 天,凡是母液浸泡过的焊缝都出现了腐蚀性裂纹,最严重的是贯穿性裂纹,出现裂纹的焊缝能达到焊缝总数的61 %。长铝公司氧化铝厂1 100 m2 蒸发器加热室的上下封头、循环弯管、蒸发室第三视镜以下部分母液所在之处的焊缝都时常出现腐蚀性裂纹。许多铝厂的蒸发器都经常有类似现象发生,造成了金属材料重大损失,影响了设备的使用寿命,而且使得设备的检修周期缩短,增加了辅助时间和修理费用。同时,由于应力腐蚀现象的发生,使得设备及管道的跑、冒、滴、漏现象甚为严重,原料和成品大量损失,影响了产品质量,污染了环境;有的还引起爆炸,出现灾难性的事故。可见,对蒸发器发生应力腐蚀断裂的研究和控制是一个十分迫切的问题。
二、应力腐蚀裂纹的特征 1. 应力腐蚀的基本概念 应力腐蚀是指金属材料在拉应力和腐蚀性介质联合作用下产生的一种腐蚀破坏,其结果使金属材料产生腐蚀裂纹,甚至突然破裂。化工设备在焊接加工过程中和工作承载过程中都会产生应力,这些应力作用结果引起设备金属材料内部晶格的扭曲,或产生微裂纹,从而降低了这些部位的电极电位,与电解液接触时,这些部位就形成腐蚀微电池的阳极,造成腐蚀。随着腐蚀的进行,裂纹很快扩展,以致产生破裂。这种由于应力和腐蚀性介质联合作用下产生的腐蚀叫应力破坏腐蚀。 2. 应力腐蚀裂纹的特征 应力腐蚀的裂纹有沿晶发展和穿晶发展两种基本途径,宏观上应力腐蚀裂纹基本上垂直于拉伸应力。氧化铝蒸发器的应力腐蚀裂纹在环焊缝的地方呈辐射状;在直焊缝的地方呈蜈蚣状,均沿垂直于焊缝的方向上连续扩展;深入到金属内部的应力腐蚀裂纹,就如植物根须一样由表面向纵深发展。应力腐蚀的断口是典型的脆性断口。一般情况下,低碳钢、低合金高强度钢等大多属沿晶断裂,裂纹大致垂直于拉应力方向,由晶间向纵深发展,这类沿晶断裂在电子显微镜下观察为冰糖状花样。
三、应力腐蚀裂纹产生的原因 1. 产生应力腐蚀裂纹的匹配性 金属材料在腐蚀介质与拉应力同时作用下不一定都会发生应力腐蚀,例如碳钢在稀硫酸中即使在拉应力作用下也不会产生应力腐蚀,只会产生极快的均匀腐蚀。这说明金属在某种介质中是否会产生应力腐蚀具有明显的选择性。即材质与介质有一定的匹配性,也就是某种材料只在某些介质环境中才产生应力腐蚀裂纹。一些易使常用金属材料产生应力腐蚀开裂的介质见表1。
表1 最易于产生应力腐蚀开裂的环境匹配示例
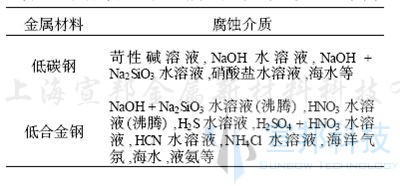
2. 蒸发器发生应力腐蚀的机理 应力腐蚀裂纹的产生受材质、腐蚀介质和临界拉应力3 个因素制约,目前,从电化学方面考虑,应力腐蚀裂纹大体分为2 类,即阳极溶解腐蚀(简称APC) 和阴极氢脆开裂(简称HEC) ,多数情况下是两者共存。 低碳钢在浓度不超过30 %的碱溶液中是稳定的,这是由于在金属表面生成了一层由氢氧化铁和氢氧化亚铁组成的不溶性的腐蚀产物,它与金属表面结合紧密故起保护作用。如果没有应力作用,就不会发生腐蚀破坏,如图1 (a) 所示。但是如果有应力作用,特别是残余应力叠加或存在应力集中部位,就会产生局部滑移,形成滑移台阶面,破坏保护膜,露出新的金属表面,如图1 (b) 所示。由于滑移台阶附近的滑移带中堆集了大量位错,甚至伴随着孔洞、少量合金元素原子和杂质原子在滑移带上析出等,而使滑移台阶处金属活化,加速化学溶解,并形成电化学腐蚀的阳极,保护膜未破坏区则成为阴极。在发生表面滑移的阳极溶解时放出的电子直接流入阴极,被电解质中的H+ 所吸收而成为H ,这样促使电子不断流动,加快腐蚀速度,就造成吸氢腐蚀。
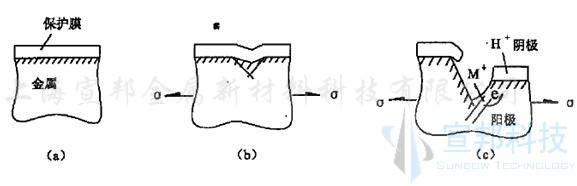
图1“滑移阶梯”示意 a金属表面生成一层保护膜;b金属在拉应力作用下产生滑移变形; c金属产生较大的“滑移阶梯”,附近保护膜被拉破
3. 影响应力腐蚀开裂的因素 影响应力腐蚀开裂的因素有金属材质、腐蚀介质、温度、浓度以及应力状态等。 (1) 材质因素。主要是材料的化学成分和组织性能的不均匀性,由于其电极电位不同,易形成微电池,故与一定介质(电解质) 匹配时就会产生电化学腐蚀。 (2) 应力因素。主要是工作应力和残余应力(包括焊接、加工及安装残余应力) ,由于它们的叠加,产生局部滑移,从而破坏钝化膜,使金属发生应力腐蚀。在由应力腐蚀造成的断裂中,残余应力造成的危害比较明显。调查发现,因焊接和加工的残余应力所引起的事故,占应力腐蚀断裂事故的80 %以上。由于许多应力腐蚀是在无外加载荷的情况下发生的,实际上是由焊接残余应力中的拉应力在起作用。有时焊接残余应力最大值可能达到材料屈服点σs 的程度。因此焊后消除残余应力是防止应力腐蚀破坏的有效措施。另外裂纹内的腐蚀产物有时也会产生巨大的应力,促使裂纹胀开,加速裂纹扩展过程。 (3) 温度和浓度的影响。例如,对碳钢和低合金钢焊制的化工容器不进行消除应力热处理时,则在NaOH溶液中的使用温度越高,焊缝的应力腐蚀就越严重。 总之,蒸发器在焊接过程中不可避免地会产生残余应力,所以对于焊接构件蒸发器来讲,即使在无载情况下放置,只要存在适当的腐蚀介质,就有可能产生应力腐蚀裂纹,而且焊接接头属非均质材料,又是各种应力叠加的集中处,其表面脆化层易剥落成为微缺陷区,是应力腐蚀的微裂纹源。所以其耐应力腐蚀开裂的能力远比相对均质的母材金属差得多,这就是氧化铝厂蒸发器发生应力腐蚀都是在有焊缝地方的重要原因。这一点必须引起足够的重视。 四、 控制产生应力腐蚀的措施 在生产条件下如何控制蒸发器的应力腐蚀是一个较难的课题。由于影响应力腐蚀开裂的因素是多方面的,所以控制途径也是多方面的,可以从设计、制造和管理方面同时进行。 1. 设计方面 (1) 选材。应根据应力腐蚀介质和材料的组合,考虑腐蚀介质的特性、浓度、腐蚀机理、温度和压力来选材。随着金属材料强度级别的提高,发生应力腐蚀开裂的危险性也增加了,所以对于有应力腐蚀危险的氧化铝蒸发器,要限制其基本材料的强度水平。但同一强度级别不同合金系列的钢材,抗应力腐蚀开裂的倾向也可能相差很大,在选材时应充分注意,要对具体情况分析后确定选材。工程上常使用的材料和容易使之发生应力腐蚀开裂的介质如表1所示。 (2) 避免应力集中。要求有正确的结构设计,使结构的应力均匀分布,没有应力集中源,同时将结构上的一切拐角、死角、缝隙等容易使附着介质发生浓缩的部位加以改进。设计焊缝要注意不留缝隙,例如断续焊宜改为连通焊,单面焊宜改为双面焊,以防止应力腐蚀事故。 2. 生产制造方面 (1) 冷作变形的控制。在制造中通常要进行冲剪、弯曲等冷作工艺,焊后要进行冷校正。因为冷变形会产生大的残余应力和硬化,都增加了应力腐蚀倾向,所以必须尽可能地减少冷作变形。 (2) 焊接材料的选择。尽管母材的耐应力腐蚀能力很强,但若焊接材料选用不当,同样会使设备发生早期失效,因此焊接材料对母材的匹配是很重要的。要通过了解结构的工作条件,熟悉介质的腐蚀 特性,认真分析合金系统各金属元素的特性来选择焊条。一般来讲,根据腐蚀介质的不同,焊缝金属的化学成分和金相组织应尽可能与母材相一致,否则就会带来不良的后果。 (3) 焊接工艺控制。为防止应力腐蚀开裂,在焊接工艺方面要制订合适的焊接规范和焊接顺序,过大的线能量会使晶粒粗化,也会大大增加应力腐蚀倾向。要求不发生严重的热影响区硬化、晶粒长大和各种脆化,同时降低构件的残余拉应力。实践证明,热影响区硬度越高,产生应力腐蚀开裂的临界应力越要降低,热影响区组织对应力腐蚀开裂倾向有相当大的影响。从低合金钢热影响区的组织看,大体按下列次序而增大应力腐蚀开裂倾向:球状珠光体→层状珠光体→500 ℃回火马氏体→马氏体。 (4) 焊接残余应力及应力集中源的控制。焊接残余应力是产生应力腐蚀的主要原因之一,焊接时强制组装所引起的装配应力也会促进应力腐蚀开裂,因此合理施工,用各种方法尽量减少或消除结构中的残余应力,对控制应力腐蚀开裂有重要作用。重要的焊接结构一般都要经过消除应力处理,还要特别注意消除工艺过程中的各种伤痕,如拉筋伤痕、锤击伤痕、非焊接区的引弧疤痕等,这些伤痕都会成为应力腐蚀的裂源,必须加以避免。所有这些措施的实施将同时提高结构的疲劳强度。 (5) 焊后消应。为了减少、消除焊接接头应力集中处的残余拉应力,应对蒸发器的蒸发母液所到之处的焊缝全部进行焊后消应处理,从而减少应力腐蚀的危害。
五、 结束语 氧化铝厂蒸发器在焊缝地方发生应力腐蚀裂纹的主要原因有两方面:一是蒸发器的材质与易产生应力腐蚀裂纹的工作介质环境相匹配,二是在焊缝的地方存在焊接残余拉应力。由此看来,为了既经济又安全,只有控制焊缝的残余应力。近年来发展起来的超声冲击应力消除技术是一种非常灵活的焊接应力消除技术,被誉为目前最彻底消除残余应力并产生出理想压应力的时效方法。经过超声冲击后,焊缝的应力状态可以得到很好改善,防止或减缓应力腐蚀问题的出现。这种方法是防治氧化铝厂蒸发器发生应力腐蚀裂纹的重要途径之一。
附录:
超声冲击技术是以超声波为动力,冲击处理焊趾,提高焊接接头及结构疲劳强度,由世界闻名的乌克兰Paton焊接研究所最早提出,并由Paton焊接研究所和俄罗斯“量子”研究院共同开发成功。早期主要用于消除结构中的焊接残余应力,八十年代开始向提高焊接接头疲劳强度的方向发展。1996年在IIW年会上曾报道,在西伯利亚的某金属结构厂开始尝试应用该方法。1997年,在国家自然科学基金资助(编号:59575061)及我国著名焊接结构专家霍立兴教授指导下,由天津大学焊接工程技术研究所的王东坡博士研制成功了我国第一台超声冲击装置,该装置也是世界上最早见于报道的基于压电技术的超声冲击设备,从此超声冲击技术出现压电和磁致伸缩(俄罗斯和乌克兰)竞相发展的新格局。 1998年,王东坡博士完成冲击头、换能器的制作和电源主电路的设计,2000年实现频率锁相跟踪,第一代机器HJ-Ⅰ型超声冲击设备诞生。该机型在世界上首次实现了压电式换能器超声冲击装置,将核心部件能量转换效率从40%提高到85%以上。2000年起,研发集中于解决功率输出稳定性问题,2003年,第二代机型HJ-Ⅱ型超声冲击设备研制成功。从电路部分分析,HJ-Ⅱ型超声冲击机拥有的一套完善的频率跟踪系统,这也是超声冲击设备的控制核心之一。试验验证HJ-Ⅱ型超声冲击机可以保证不间断工作5小时以上,整个系统仍处于良好状态。2004年,开始研制第三代机器,该型号采用全数字化控制系统,不但保证了频率跟踪的稳定性和机器的抗干扰性,而且跟踪范围更宽,并且机器的各种参数指标可以通过简单清晰的人机交互界面设定。通过优化机器的功率控制部分,提高了电源的工作效率,输出功率进一步提高,并且通过与自动控制装置的结合可以实现自动处理。第三代机器HJ-Ⅲ型超声冲击设备已于2007年基本定型。2007年,上海宣邦金属新材料科技有限公司成立,天津大学焊接工程技术研究所王东坡教授担任公司技术顾问,由此,开始了超声冲击设备市场化的新纪元。
|